Advanced Fasteners and Machining Techniques for Custom-made Manufacturing
Advanced Fasteners and Machining Techniques for Custom-made Manufacturing
Blog Article
Unveiling the Details of Fasteners and Machining Procedures for Ideal Performance
In the world of design and manufacturing, the choice of fasteners and the details of machining processes play an essential function in figuring out the utmost performance and durability of an item. From the seemingly uncomplicated task of picking the best sort of fastener to the facility precision machining methods utilized, every step in this procedure demands thorough attention to information. As we embark on this expedition into the globe of fasteners and machining, we will certainly uncover the refined yet crucial variables that can substantially impact the effectiveness and top quality of the end product, clarifying the frequently forgotten aspects that can make all the difference in attaining optimal performance.
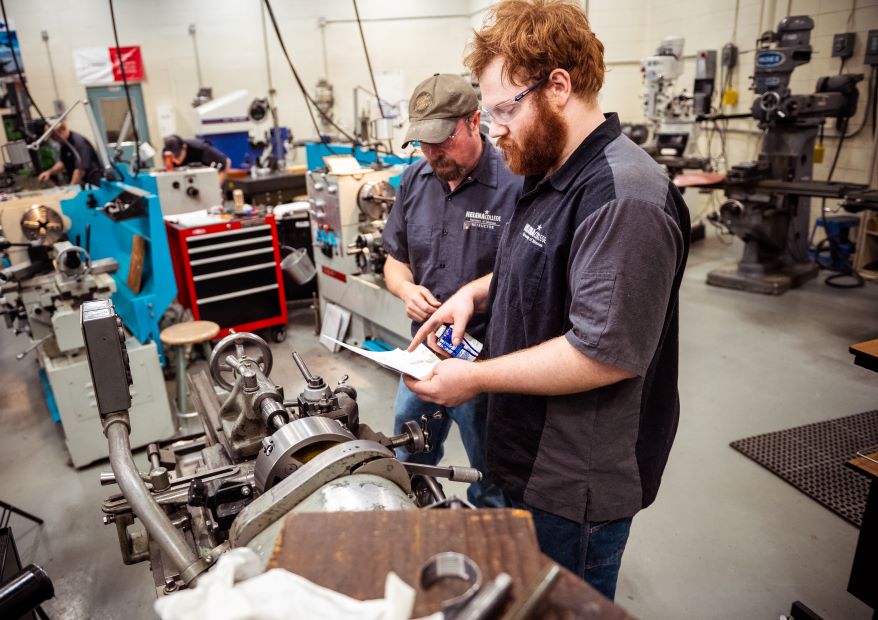
Importance of Proper Bolt Choice
Choosing the appropriate bolts is critical in making certain the architectural stability and longevity of any kind of mechanical setting up. Fasteners play a basic role in holding parts with each other securely, with the right selection contributing significantly to the general performance and integrity of the assembly. When choosing fasteners, factors such as product compatibility, environmental problems, load-bearing capability, and convenience of setup must be meticulously thought about to assure ideal efficiency.
Improper fastener option can result in an array of problems, consisting of loosening, deterioration, and even architectural failure. Utilizing bolts that are not suited to the certain requirements of the setting up can compromise its performance and pose security threats. Designers and designers need to diligently assess the application requires and pick bolts that meet or surpass the needed criteria and specifications.
Additionally, the appropriate bolt option procedure involves evaluating the joint style, prepared for loads, vibration levels, and potential thermal growth or contraction to guarantee that the selected bolts can hold up against the operating problems effectively. By prioritizing appropriate fastener choice, makers can improve the top quality, resilience, and performance of their mechanical assemblies.
Types and Characteristics of Bolts
An important element of mechanical assemblies hinges on comprehending the varied kinds and distinct features of fasteners used in different industrial applications. Fasteners are essential parts that hold structures with each other, guaranteeing stability and capability. There is a wide variety of bolts offered, each created for certain objectives based upon the application requirements. Common types of bolts include screws, bolts, nuts, pins, rivets, and washers.
Screws are threaded fasteners that are generally utilized to join two or more elements together. Screws are similar to screws yet are usually used with a nut to develop a protected joint. Nuts are inside threaded fasteners that mate with screws to hold components with each other. Washers are slim plates that distribute the tons of a bolt, stopping damage to the material being attached. Rivets are long-term bolts that are hammered or pressed right into area. Pins are used for positioning or to secure parts temporarily.
Recognizing the features of each kind of fastener is important for selecting the ideal one for a specific application, ensuring optimum efficiency and integrity of the mechanical setting up. Fasteners and Machining.
Accuracy Machining Methods for Performance
The detailed style needs of different bolts require using precision machining techniques for ideal effectiveness in manufacturing processes. One of the key methods made use of in precision machining is Computer system Numerical Control (CNC) machining, which enables high levels of precision and repeatability in the production of bolts.
In addition to CNC machining, various other accuracy methods such as grinding, milling, and transforming are commonly utilized to achieve the tight resistances needed for fasteners. These methods permit makers to develop fasteners with smooth surfaces, specific dimensions, and high structural honesty. By making use of precision machining methods, suppliers can enhance the high quality of bolts, lower material waste, and boost total production effectiveness. In addition, using advanced machining processes assists make certain that fasteners meet market requirements and customer expectations for performance and dependability.

Elements Affecting Machining Process Efficiency
Various variables play a significant function in figuring out the performance of machining processes in the production of bolts. The initial important factor is the selection pop over here of cutting tools. Picking the ideal devices based upon the product being machined, desired finish, and reducing rates can substantially affect the effectiveness and quality of the machining process. In addition, the cutting criteria such as reducing speed, feed rate, and depth of cut are crucial variables that affect performance. Fasteners and Machining. Enhancing these parameters based on the certain needs of the bolt being produced is essential to achieving specific and economical machining.
Machine rigidness and stability additionally play a critical role in identifying machining procedure efficiency. A secure device with marginal vibrations can enhance accuracy and protect against tool wear, causing far better total performance. The ability and experience of the device driver can not be ignored. A knowledgeable operator can make real-time changes, troubleshoot problems successfully, and ensure that the machining procedure runs efficiently, ultimately affecting the last quality of the bolt.
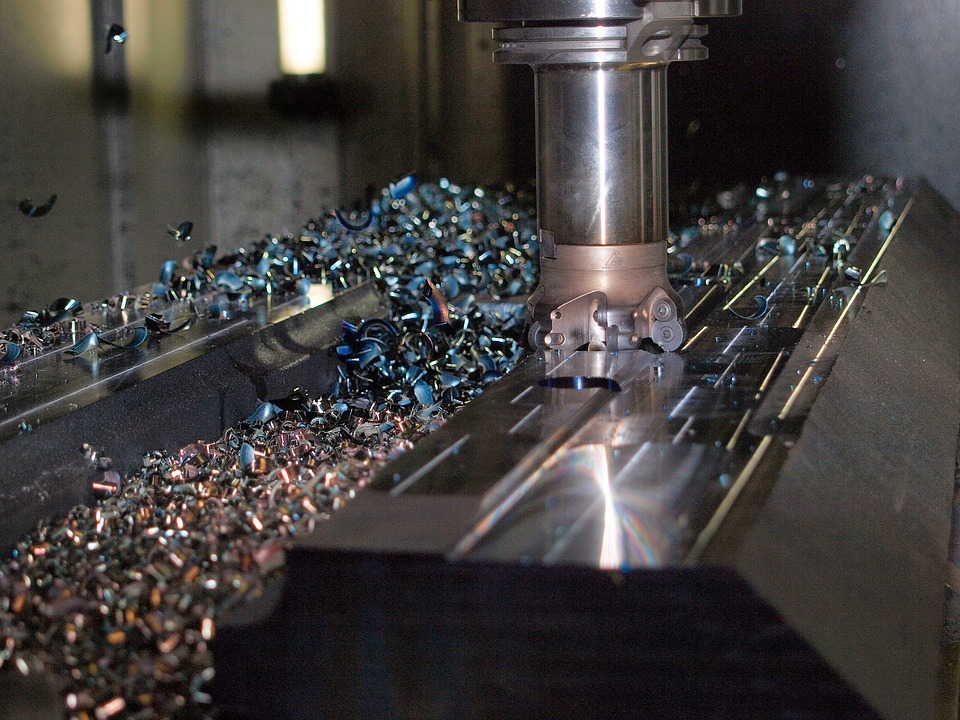
Quality Assurance Procedures in Production
Variables influencing machining process efficiency, such Home Page as reducing device choice and equipment stability, directly effect the execution of quality control steps in manufacturing. Normal upkeep of machining devices is additionally vital to promote top quality control. By adhering to stringent top quality control actions, suppliers can improve consumer contentment, construct a reputation for dependability, and ultimately achieve ideal efficiency in their machining procedures.
Verdict
To conclude, selecting the right fasteners and utilizing precision machining techniques are essential for ideal performance in producing procedures. Comprehending the kinds and characteristics of bolts, together with aspects influencing machining procedure efficiency, can cause improved effectiveness and quality assurance actions. By taking useful content note of these details, manufacturers can achieve greater degrees of efficiency and dependability in their items.
In the world of design and manufacturing, the choice of fasteners and the complexities of machining procedures play a crucial duty in figuring out the utmost efficiency and toughness of a product (Fasteners and Machining). One of the primary methods made use of in precision machining is Computer Numerical Control (CNC) machining, which enables high levels of accuracy and repeatability in the production of bolts. The use of advanced machining procedures assists guarantee that bolts satisfy industry criteria and client assumptions for performance and reliability
In final thought, selecting the ideal fasteners and making use of accuracy machining methods are necessary for optimum performance in making processes. Recognizing the kinds and features of fasteners, along with variables influencing machining procedure efficiency, can lead to improved efficiency and high quality control actions.
Report this page